Meet the Toronto startup helping bring 3D printed buildings to Canada
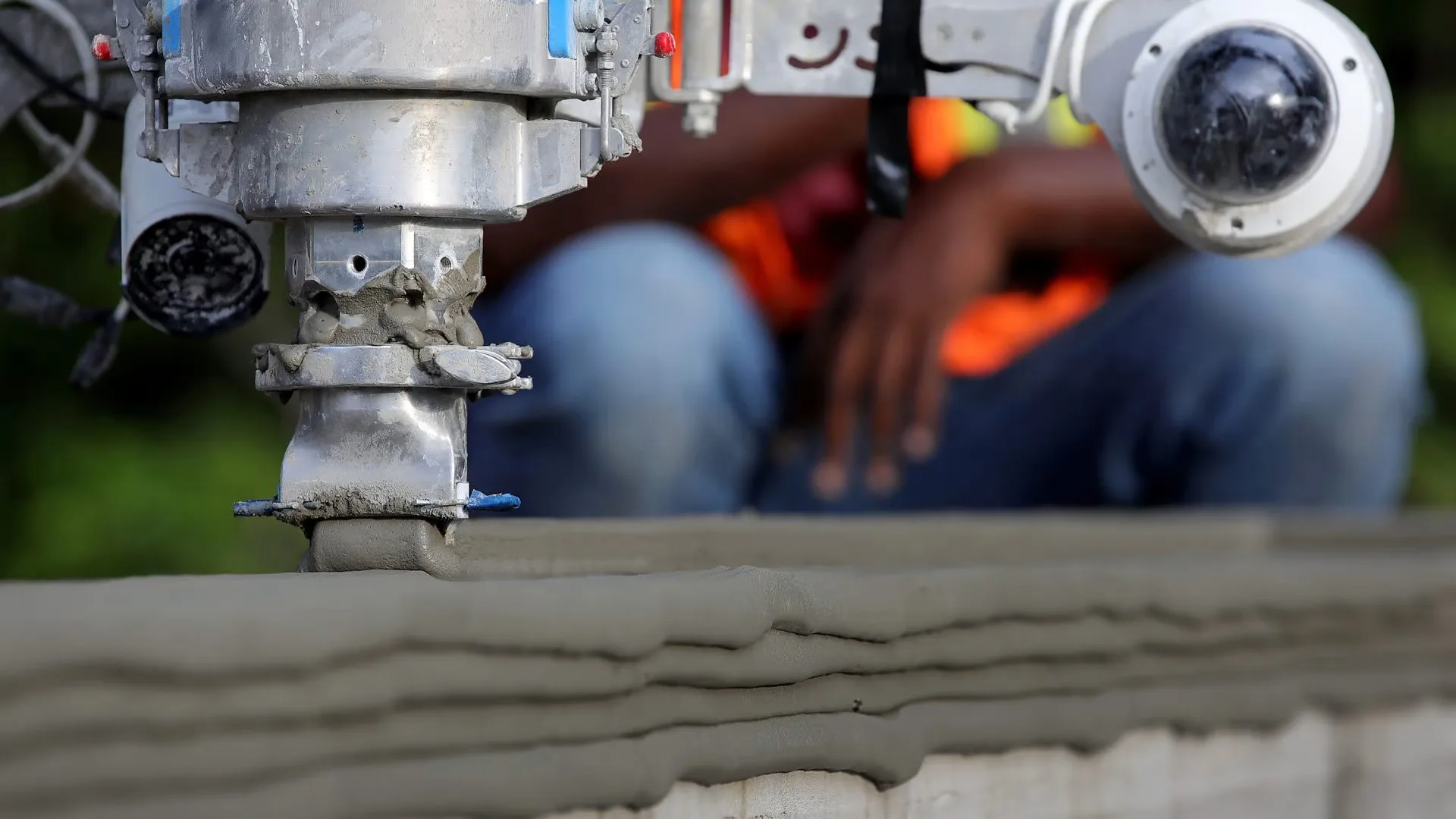
Ontario construction startup Leostar Development Group Inc is on the tip of bringing 3D printed housing to Canada through Printerra Inc.
While the 3D printing of buildings has been taking place internationally for many years in regions like Europe, the Middle East, and Asia, Canada is still in the early days of adopting the technology. As recent as 2022, Canada’s first 3D printed building was completed as part of a project for Habitat for Humanity.
This type of slow adoption of new technology is a common trend in the construction industry, which has been slower than many other sectors to adopt digital innovation.
Founded in 2016, Leostar is a commercial and residential construction company that wants to put innovation at the forefront of what it does. It is set to be one of the first companies in Canada to utilize and implement the standard for 3D construction printing technology (3DCP).
3D printed buildings are changing the construction world by offering a faster, cheaper, and more sustainable alternative to traditional building methods. The buildings are created by large 3D printers using concrete that is then printed in layers until the building shape emerges. The concrete used in 3D printing is a special mix that ensures the material can flow easily through the nozzle of the printing equipment.
One of the many benefits of 3DCP is that it eliminates the need for casting concrete into molds or framework, and its curing time is quicker. This allows for concrete work to be completed within hours rather than days.
Leostar co-founders Leigh Newman and Yafes ‘Nick’ Gabuji first learned about 3DCP two and a half years ago. “During our initial online research, we noticed that there was a workforce shortage of skilled trades and subcontractors, there was also a huge housing demand, especially in long term care and affordable housing,” says Newman. It was then that Leostar recognized the inherent demand for housing, and the unique opportunity for innovations like 3DCP. With that in mind, Newman and Gabuji created Printerra, the 3D printing arm of Leostarin 2022. Leostar has three companies overall, which reflect its three main focus areas: infrastructure work, indoor construction, and 3D printing.
Printerra utilizes 3D printing machines created by Cobod, the company that built one of Europe’s first 3D building in 2017. Printerra is using Cobod’s machines to print here in Canada, and is currently setting up its 3D printer at York University as part of a collaborative Research and Development project with the Lassonde School of Engineering to 3D test print precast components. In June, Printerra is scheduled to print Canada’s first two- story garden suite in Scarborough.
3D concrete printing is not the only way that the Leostar group of companies are looking to be innovative. Newman says with Leostar being a newer company in the construction industry, it has a “younger, or more progressive outlook” when compared to some of the more established construction companies that tend to follow the norm, and shy away from innovation. “What it really comes down to is trying to adapt as much technology and innovation as possible into an industry that has just been so reluctant to change,” says Newman.
On that journey, Leostar had a hard time finding enterprise resource planning (ERP) tools. With three different companies, various contracts workers, and all the varying and complex construction planning being done, Leostar has not been able to find existing ERP software that meets its needs.
So, the company started tracking everything using an Excel spreadsheet. Then it learned of the Ontario Centre of Innovation’s Digitalization Competence Centre (DCC). DCC is Ontario’s knowledge centre focused on driving the digital modernization of Ontario small and medium enterprises (SMEs). It helps SMEs with digital literacy through both education, training, and adoption, and offers grants to support adoption of new digital technologies.
Leostar has received funding through DCC to develop a Digital Modernization and Adoption Plan (DMAP) that will help it figure out its ERP needs. The goal is to ensure that Leostar can easily manage everything across all three of its companies.
Newman’s goal is to ensure that Leostar has a reliable system that will allow it to scale its businesses and ensure it can bring more 3D printed buildings to Canada.
Alicia Pereira,
Director, Communications & Strategy
Media essentials including backgrounders, logos, photos and links to OCI publications.
Stay up-to-date with the latest OCI news and events right in your inbox!